Working principle and function of electric air conditioning compressor
Electric bus air conditioning compressors are an important component in zero-emission
electric bus air conditioning systems used in public transport around the world. The
low/high-pressure electric compressor works with other components such as the condenser coil, expansion valve, and thermostat to maintain a comfortable cabin temperature environment for passengers and drivers.
The primary function of this compressor is to pressurize and circulate the refrigerant fluid throughout the AC system, converting it from gas to liquid and back to gas. As the gas absorbs heat from the inside of the bus and releases it to the outside, the compressor helps create the proper temperature balance for everyone's comfort.
Advantages of Electric Bus AC Compressor
As a sustainable and environmentally friendly mode of transportation, electric buses have received widespread attention and adoption worldwide. With the development of electric buses, major advancements have been made in various components of their systems, including air conditioning compressors. Air conditioning compressors for electric buses play a pivotal role in ensuring passenger comfort and efficient operation of the air conditioning system.
Electric bus air conditioner compressors are more energy efficient and the electric motors powering these compressors are designed to optimize energy consumption, thereby reducing power losses and increasing overall system efficiency. By reducing energy consumption, air-conditioning compressors for electric buses help extend the vehicle's range and improve energy efficiency.
Noise reduction:
Electric bus air conditioning compressors run quietly, offering significant advantages over conventional engine-driven compressors. The absence of an internal combustion engine and a belt drive mechanism results in lower noise levels inside and outside the bus cabin with reduced resonance. This results in a more peaceful and comfortable passenger experience and reduces noise pollution in urban environments.
Upgraded performance and control:
Electric compressors offer better control and responsiveness than engine-driven compressors. Their motor-driven design allows precise regulation of compressor speed, resulting in faster cooling and better internal temperature regulation. This feature ensures optimum comfort for passengers while reducing energy waste.
Maintenance and Reliability:
Electric passenger car air conditioning compressors typically require less maintenance than engine-driven compressors. They have fewer moving parts, reducing the chance of mechanical failure. Additionally, since they are not subject to the same vibration and heat generated by internal combustion engines, electric compressors tend to last longer, reducing maintenance costs for bus operators.
Integration with regenerative braking:
Electric buses typically utilize regenerative braking systems to recover and store energy during deceleration. Electric bus air conditioning compressors can be integrated with these systems, allowing the recovered energy to power the compressors, thereby reducing the overall energy consumption of the air conditioning system. This integration improves the energy efficiency of the bus and contributes to its sustainability.
Basic characteristics of EV air conditioner compressor
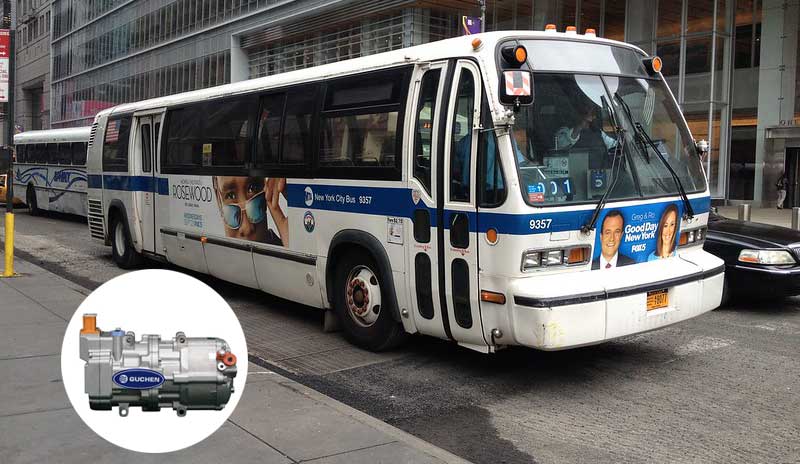
1. Energy-efficient design: Since electric buses rely on batteries for power, their components need to be highly efficient to save energy. As a result, electric bus air conditioning compressors feature intelligent controls, variable frequency drives, and high-efficiency designs to maximize cooling output while minimizing energy consumption.
2. Anti-vibration technology: Compared with private cars, large vehicles generate more vibration, so the electric bus air-conditioning compressor integrates an anti-vibration system to ensure smooth operation and extend the service life of components. These measures may include elastic mounts, rubber isolators, or balancing strategies.
3. Environmental tolerance: Electric buses operate outdoors in harsh urban and suburban environments. Therefore, electric bus air conditioning compressors must be able to withstand extreme temperatures, humidity levels, corrosion, salt spray, pollution, and other environmental hazards that are prevalent along the way. This requires building them using durable materials, sealing techniques, and finishes that can withstand long-term exposure.
4. Custom compatibility: Each electric bus model has its specific AC architecture and integration points for major components. Therefore, electric bus air conditioning compressors must be customized to accommodate unique chassis layouts, size constraints, connection interfaces, and signal controls.
What is the point of using an electric compressor?
Environmental Benefits:
The adoption of electric bus air conditioning compressors can bring significant environmental benefits. By eliminating direct emissions, these compressors help improve air quality and reduce the carbon footprint of public transport. The use of air conditioning compressors in electric buses plays a vital role in achieving sustainable transport solutions.
Sanitation and Comfort:
Electric passenger car air conditioning compressors enhance passenger comfort by providing efficient and reliable cooling without the noise and vibration associated with traditional compressors. This helps provide passengers with a pleasant and comfortable commute, especially in hot weather conditions. In addition, the elimination of air-conditioning system exhaust emissions improves the air quality inside the bus, promoting public health and well-being.
Technological innovation and industry growth:
The development and implementation of air conditioning compressors for electric passenger cars have stimulated technological innovation and growth in the transportation industry. Manufacturers and suppliers invest in research and development to improve the efficiency, performance, and durability of electric compressors. This has led to advances in motor design, control systems, and refrigerant technology.