Non-independent truck refrigeration systems provide maximum quality at a reasonable price.
, are designed to provide the right temperature for trucks transporting perishable goods and medical supplies that require cryogenic refrigeration.
These devices are critical to industries such as food transportation, pharmaceuticals, and other temperature-sensitive products. Here are some key features of truck refrigeration units:
Different models of truck refrigeration units can provide different cooling capacities to meet the specific requirements of different cargo sizes and temperature ranges. Cooling capacity is usually measured in thermal units per hour (BTU/hr) or kilowatts (kW).
The TRU is equipped with an advanced temperature control system that precisely regulates the internal temperature. This ensures that the cargo remains within the required temperature range throughout the transit.
The TRU can be powered by a variety of power sources, including a truck engine (using a direct drive system), a stand-alone diesel engine (stand-alone unit), or an external power source.
In order to maintain the required temperature in the cargo area, the truck refrigeration unit is constructed of high-quality insulation. These materials effectively reduce heat transfer from the external environment, ensuring efficient cooling and reducing energy consumption.
The TRU contains fans, vents, and ductwork to aid in airflow and ensure consistent temperature control.
Monitoring and Control: Modern truck refrigeration units are equipped with sophisticated monitoring and control systems. These systems provide real-time information on temperature, humidity, system performance, and any potential problems.
Choosing the right truck chiller model to ensure your cargo kept at a safety temperature during transport. It is critical to your present business and future growth.
◆ Hot gas defrosting (Auto. /Manual)
|
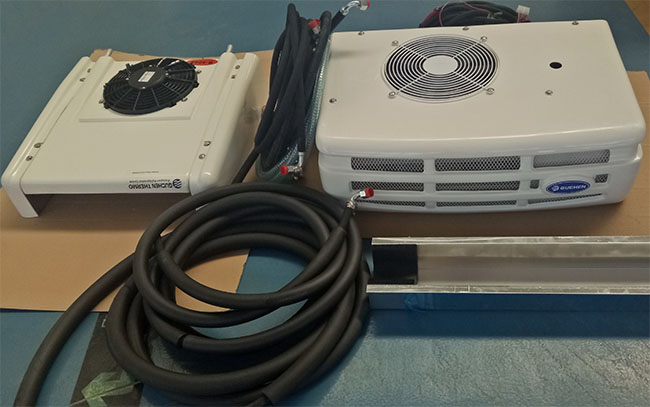 |
Model |
TR-200 small truck refrigeration unit |
Type |
chiller & freezer system |
Applied for |
6m³ - 15m³ box volumes or 2m small refrigerated trucks |
Refrigeration capacity |
2,200W |
Temperature range |
-18℃ to +30℃ |
Usage |
used to transport frozen or fresh cargoes |
Medium Truck Refrigeration Units ( frozen: -20℃ to 30℃ )
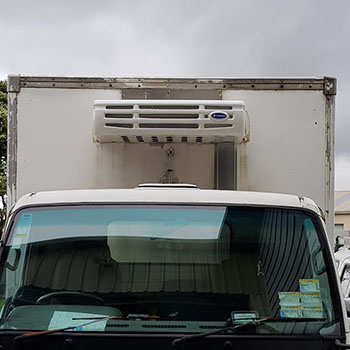 |
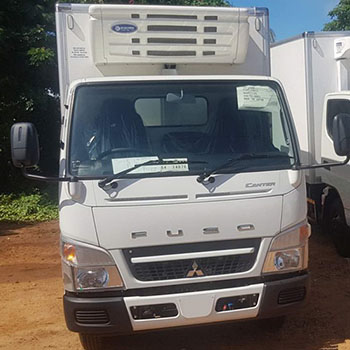 |
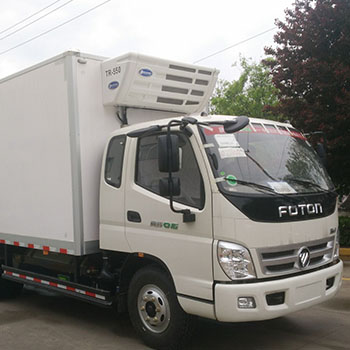 |
TR-350 |
TR-450 |
TR-550 |
15~25m³ medium refrigerated trucks |
18~25m³ container volumes |
20~30m³ refrigerated truck bodies |
4.2m refrigerated trucks |
4.5m |
5.5m |
3815W cooling capacity |
4100W |
5800W |
front mount |
front mount |
front moun or undermount |
used to transport frozen or fresh goods |
As the best truck refrigeration unit manufacturer in China, Guchen Industry supplies 3 models of meidum-size truck freezer systems: TR-350, TR-450, and TR-550 unit. No matter what your truck volume is, you can always find a suitable refrigeration unit at Guchen.
Need any assistance? Please mail to
info@guchen.com
Large Truck Refrigeration Units ( frozen: -20℃ to 30℃ )
TR-600 truck freezer units are suitable for high temperature up to 50℃, with 6050W cooling capacity at 0 ℃, can make temp. range from -30 to 30℃ to keep foods frozen or fresh, applying in 30~40m³ big refrigerated truck bodies.
With 5800W cooling capacity, TR-650 vehicle refrigeration units are suitable for lager refrigerated truck bodies with 22-35 m³ volume and 6.5m truck bodies’ length.
TR-760 transport refrigeration units have 7225W cooling capacity, which can make 35-45 m³ refrigerated truck bodies temperature down to -20℃. With condenser front mounted or under mounted, suitable for most of truck conditions with 7.6m length.
TR-860 refrigerator unit for truck is suitable for 40-50 m³ refrigerated truck bodies, with 7850 W cooling capacity, can make 8.6m length truck container temperature range from -20℃ to 30℃ on the road.
TR-960 refrigeration unit for truck with the biggest cooling capacity (8425 W) in Guchen’s direct engine driven refrigeration units, which are able to make 60m³ refrigerated truck box with 9.6m length temperature down to -20℃ on the road.
The Difference Between Direct Drive and Diesel Drive Truck Refrigeration Units
The main difference between direct-drive and diesel-driven truck refrigeration units is how they are powered.
Direct Drive Truck Refrigeration Units:
Direct-drive truck refrigeration units are powered by the truck engine. These units are usually integrated with the truck's existing engine and use the engine's power to run the refrigeration system. Here are some key features:
Power source: The direct drive is connected to the truck's powertrain and uses the mechanical energy of the engine to drive the refrigeration compressor and other components.
Fuel consumption: Direct drives get their power directly from the truck's engine, which means they consume fuel from the truck's tank. The fuel efficiency of a truck engine directly affects the efficiency of the refrigeration unit.
Cooling performance: Direct drive units typically have excellent cooling due to the power provided by the truck engine. They are ideal for refrigerated car boxes that require high cooling capacity and frequent door openings.
Diesel-powered truck refrigeration unit:
Diesel-powered truck refrigeration units, also known as self-contained units, have their own separate diesel engine powering the refrigeration system. Here are the main features:
Power source: Diesel drives have their own dedicated diesel engine, usually mounted on the front or side of the truck. These engines drive the refrigeration system independently of the truck engine.
Fuel Consumption: The diesel drive has its own fuel tank and consumes diesel to power the refrigeration system.
Cooling Performance: Diesel-powered units offer strong cooling performance and are often preferred for long hauls or where the truck engine may be shut down while remaining cool.
Flexibility: Diesel drives offer flexibility as they can operate independently of the truck engine. This allows the refrigeration system to continue running even when the truck engine is not running or during breaks.
Composition structure of truck refrigeration unit
The following are key components commonly found in truck refrigeration units:
Compressor: A compressor is an important component that circulates and compresses refrigerant gas, increasing its pressure and temperature.
Condenser: The condenser is responsible for releasing the heat of the refrigerant. It is a heat exchanger that helps transfer heat from high-pressure refrigerant to the surrounding environment.
Evaporator: The evaporator is another heat exchanger located inside the cargo area of the truck. It absorbs heat from the cargo, cooling it down.
Expansion Valve: An expansion valve, also known as a thermal expansion valve or a metering device, regulates the flow and pressure of refrigerant. It is located between the condenser and the evaporator.
Refrigerant: A refrigerant is a working fluid that undergoes a phase transition from gas to liquid and back to gas during the refrigeration cycle. It is responsible for absorbing and releasing heat, allowing the cooling process to take place.
Control Panel: The Control Panel contains the control and monitoring system for the cooling unit. Includes a variety of switches, buttons, and displays that allow operators to set and adjust desired temperatures, monitor system performance, and receive alerts or alerts of any problems or deviations.
Airflow System: The airflow system ensures proper circulation of cool air within the cargo area. Includes fans, ducts, vents and baffles to evenly distribute cooling air throughout the cargo compartment.
Insulation: Truck refrigeration units are often enclosed in an insulated enclosure or compartment to effectively reduce heat transfer between the interior and exterior environment.
These components work together to create a refrigeration cycle that extracts heat from the cargo area and releases it to the surrounding environment, maintaining the temperature needed to transport perishable goods.
How do Truck Refrigeration Units Work?
Truck refrigeration units work on the principles of thermodynamics and the refrigeration cycle. A refrigeration cycle involves transferring heat from one area to another using a refrigerant as the working fluid.
Compression: The compressor draws low-pressure refrigerant gas from the evaporator and compresses it, increasing its pressure and temperature.
Condensation: The refrigerant gas then flows into a condenser located outside the cargo area. In the condenser, the hot refrigerant gas is cooled by transferring heat to the surrounding environment.
Expansion: An expansion valve is a small orifice that restricts the flow of refrigerant, causing a drop in pressure and temperature. This allows a mixture of liquid and gas to enter the evaporator.
Evaporation: As the low-pressure refrigerant mixture expands in the evaporator, it absorbs heat from the cargo and the surrounding air. This process cools the cargo area as the refrigerant evaporates into a low-pressure gas.
Compression (again): The low-pressure gas is then drawn into the compressor to start the cycle again. The compressor increases the pressure and temperature of the refrigerant gas, starting a new refrigeration cycle.
Throughout the cycle, the components of the truck refrigeration unit work together to extract heat from the cargo area and release it to the outside environment, maintaining the desired temperature inside the truck.
The heat transfer and phase change process of the refrigerant is repeated to provide the desired cooling effect. The temperature control system in the unit monitors the temperature in the cargo area and adjusts the operation of the compressor and other components to maintain the set temperature.
The actual refrigeration system in the truck unit may have additional components, sensors, and controls to ensure efficient and precise temperature control.
Truck Refrigeration Unit Maintenance
Proper maintenance of your truck refrigeration unit is critical to ensuring its reliable operation and peak performance. Regular maintenance helps prevent breakdowns, prolongs the life of equipment, and maintains the temperature control needed to transport perishable goods.
Periodic Inspections: Perform routine visual inspections of equipment for any signs of damage, leaks, loose connections, or worn components. Check for oil leaks, refrigerant leaks, loose belts, damaged wiring, and any other visible problems. Address these issues promptly to prevent further damage.
Cleanliness: Keep the refrigeration unit clean inside and out. Remove any dirt, debris, or built-up grime from unit components, including the condenser, evaporator, fan, and air filter.
Air Filter: Check and clean the filter regularly to ensure proper airflow and prevent contamination of the evaporator coil.
Lubrication: Check the lubrication needs of unit components such as compressors and fan motors. Lubricate moving parts as recommended to reduce friction, prevent premature wear, and maintain smooth operation.
Refrigerant Levels: Monitor refrigerant levels regularly to ensure they are within the recommended range. A low refrigerant level can affect cooling performance and may indicate a leak in the system.
Electrical Components: Check the electrical connections, wiring, and control panel for any signs of damage, corrosion, or loose connections.